- Case Description
- Details of Business Model
- Impact
- Innovation
- About Pioneer
- Geography
Case Description
Waste paddy residue across Punjab and Haryana find its application in construction material. Solutions for using agricultural residue in building/construction applications are fast emerging and are driven by demand for affordable housing and natural building materials with low embodied energy. Biomass based building material made of waste paddy residue and industrial waste by-products promotes green construction by using carbon negative building material. Paddy straw brick is a type of vegetal concrete made from refused plant matter such as hemp stalk, rice straw & corn stalks etc.
GreenJams BuildTech developed these blocks as a patented technology, uses rice straw, lime sludge, steel flakes, and other industrial waste streams in different proportions to manufacture agrocrete. The strength of the concrete is based on the principle of fixing of carbon in the mineral matrix. Agrocrete comes under two versions-Solid blocks and Hollow blocks. These are lightweight, highly insulating, carbon-negative replacement of autoclaved aerated concrete (AAC) blocks and hollow burnt-clay blocks (40% higher thermal insulation, 40% lower construction cost, 20% thinner walls). They are best suited for non-loadbearing applications within structural frames in low-rise, mid-rise and high-rise structures.
Agrocrete bricks have a compressive strength of 7.5 Megapascal (MPa) compared to 3.5-35 MPa for red brick with widely used variety having strength ranging from 5-7.5 MPa, lighter density and a thermal-conductivity comparable to that of traditional bricks. The manufacturing process of these blocks is simple and is similar to the conventional brick making process, following the processes of grinding, mixing and molding then drying. The blocks take around 15-20 days to manufacture with major time spent in drying process. Due to the simple manufacturing process, it is possible to design a hyper-local model and engage rural entrepreneurs to generate green jobs.
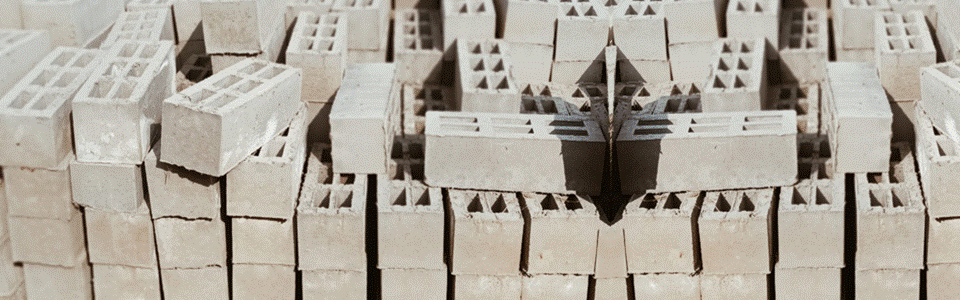
Figure: Agrocrete Bricks
Details of Business Model
- Plant Scale: 1500 blocks per day
- Capital Expenditure (CAPEX): INR 20 lakh (GreenJams BuildTech Analysis)
- Payback Period: 9 Months (CII CABL (2021) Analysis)
- Internal Rate of Return (IRR): 137% (CII CABL (2021) Analysis)
Impact
- Carbon-negative construction material
- Upto 3.5 times higher thermal insulation along with Non-flammable/fire-resistant characteristic of building material
- Upto 50% cheaper cost of construction along with faster masonry work as per few trials being done in Uttarakhand
- Compressive strength of agrocrete is comparable to clay bricks and fly ash bricks
- Water resistant with water absorption limited to less than 10%
- Higher ambient noise insulation
Innovation
Agrocrete blocks have a negative embodied carbon by virtue of the paddy residue contained in it. The carbon-negativity is further compounded by the proprietary low carbon binder. Binder is made from the industrial waste co-products of fuel ash, lime sludge and slags.
Geography
HQ: Visakhapatnam, Andhra Pradesh
Works: Roorkee, Uttarakhand